Design & engineering features
Design & engineering features
The RRS Sir David Attenborough design brief required powerful engines for navigation through ice; quiet, low-vibration operation to enable the use of sensitive acoustic instruments while underway; and adherence to strict environmental regulations.
Design and engineering features
- Engines are designed to run as silently as possible, and special attention is given to avoiding sweep-down of bubbles around the hull that could interfere with acoustic sensors
- Extremely low underwater radiated noise to avoid interference with survey equipment or disturbance to marine mammals or fish distribution
- Dieselelectric propulsion system powered by the new Bergen B33:45 engines (two nine-cylinder and two six-cylinder engines)
- 4.5m controllable pitch propellers in a Promas installation driven by two independent motors on each shaft
- Auxiliary thrusters to meet requirements for redundant propulsion and dynamic positioning
- Handling systems will cover a wide range of tasks, including subsea acoustic surveys and towing of scientific equipment with up to 12,000m of wire
- Accurate dynamic positioning system to keep the ship in place during instrument deployment using Tees White Gill bow and aft thrusters.
Environmental credentials
RRS Sir David Attenborough conforms to stringent environmental regulations that are part of the International Maritime Organisation’s (IMO) Polar Code. For more information on the Polar Code, please see the IMO’s leaflet. This vessel is the first Polar Code compliant ship built in the UK.
Under the auspices of the IMO, the International Convention for the Prevention of Pollution from Ships, or MARPOL, is the main international convention to prevent the pollution of the marine environment by ships, whether by accident or during routine operations. MARPOL guidelines exist for a range of emissions as well as the treatment of water and chemicals used on the ship, and the RRS Sir David Attenborough is designed to operate well within these and other environmental guidelines.
Main engines
The vessel has four main engines, two nine-cylinder and two six-cylinder models, built by Rolls Royce. This configuration of different engine sizes allows the ship to operate efficiently across a wide range of conditions. These engines drive four 2,750 kW asynchronous electric motors that turn two 4.5m propellers, giving the ship a cruising speed of 13 knots in open water and the ability to break through one-metre thick ice at three knots.
The four main engines are designed to operate on ultra low sulphur fuel containing less than 0.1% sulphur. This limits its sulphur oxide emissions and meets the latest MARPOL requirements for operating in sulphur emission-controlled areas.
The engines also meet MARPOL requirements to limit the emissions of nitrogen oxides (NOx). In addition, the main engine exhausts are fitted with selective catalytic reduction (SCR) units, which use urea injection to further reduce emissions of NOx to meet strict MARPOL Tier III limits.
A small harbour generator is installed, allowing the vessel to operate when in port without the main engines idling. This genset incorporates an air starting mechanism, has local control and an alarm monitoring system. The ship also has an emergency power genset with electrical and hydraulic start mechanisms.
Fuel efficiency
The ship has a hybrid electrical system consisting of large capacity batteries and main engines to allow the vessel to operate on a single main engine where otherwise two engines would be needed. This type of operation prevents the need to run engines at part-load to provide enough spinning reserve for transient spike loads. This will save a significant amount of fuel over the life of the ship. The battery system will also provide continuity of supply if a main engine trips out. The system can supply essential electrical loads during the interim period while a standby diesel alternator is starting as well as during any spike in demand.
The ship’s heating system is also designed to save power – waste heat from the engines is recycled to heat water and keep the ship’s temperature at an optimum.
Panelling around the hull has been laid internally to produce a smooth hull without steps, reducing friction and further increasing the ship’s fuel efficiency.
Preventing pollution
RRS Sir David Attenborough is fitted with an oily bilge water separator that consists of a high-speed centrifuge to reduce the oil content of the bilge water discharged to less than 5ppm, or less than 0.0005%.
Bio-degradable oils are used in the stern tube lubrication and deck hydraulic systems.
Sewage treatment
Two sewage treatment plants will be fitted to the vessel, each capable of treating black water (sewage) and grey water (other domestic wastewater) to meet the discharge standards required by MARPOL and the US Coast Guard, and to achieve Lloyd’s Register ECO notation. In areas such as the Antarctic, where zero discharge of sewage is permitted, holding tanks sufficient for 45 days are provided.
Ballast water treatment
Ballast water improves ships’ stability and balance when empty or when cargo cannot be balanced across the hold. The ballast water system on the RRS Sir David Attenborough is fitted with an approved treatment plant in accordance with the IMO’s International Convention for the Control and Management of Ships’ Ballast Water and Sediments. It controls the transfer of harmful aquatic organisms and pathogens through the ship’s ballast water system into the ocean. The treatment plant was specified to meet these requirements without discharging chemicals.
Protection from marine growth
The hull of the ship is coated with a non-toxic paint that provides a hard, impermeable and impenetrable coating which, along with manual removal of fouling at an early stage, offers long-lasting protection for the hull without the use of chemicals.
The internal sea water systems on board are protected by an electro-chlorination unit that uses sodium chloride (salt) and an electrolyser to generate sodium hypochlorite – or ‘bleach’. This chemical prevents the growth of marine organisms in the ship’s cooling systems as this would reduce the efficiency of cooling, providing a risk to the engines. Once discharged overboard, the sodium hypochlorite decomposes to form harmless and naturally occurring products – salt and oxygen.
Noise
The vessel meets strict requirements for internal and underwater radiated noise limits. This is important for deploying and operating sensitive acoustic and seismic equipment, and will also achieve the Lloyd’s Register Notation for Crew Accommodation Comfort.
For underwater radiated noise, the vessel has been designed to achieve a DNV-GL Silent (R) notation during surveys at speeds up to and including 11 knots, and a DNV -GL Silent (S) notation whilst towing seismic equipment at six to eight knots in calm seas.
Green Passport
RRS Sir David Attenborough has a Green Passport, facilitating the application of the IMO Guidelines on Ship Recycling. This document is produced by the shipyard at the construction stage and contains an inventory of all materials used in the construction of the ship. It’s produced in a format that allows any subsequent changes in materials or equipment – for example, during a refit – to be recorded. This information is useful for recycling and safe disposal purposes at the end of the ship’s life.
Commissioned by
Built by
Operated by
Share this
Featured
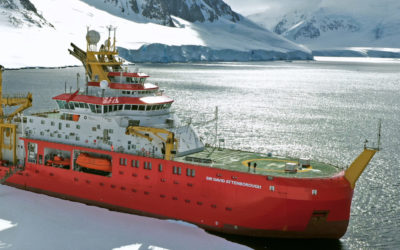
RRS Sir David Attenborough
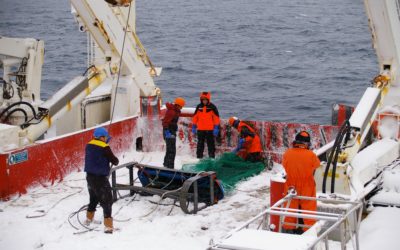
A new polar research ship for Britain: project delivery
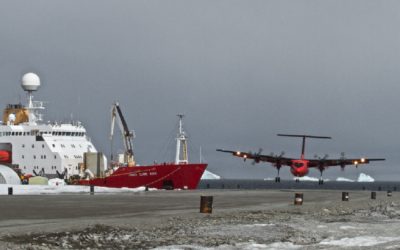