Benefits of 3D printing on board the RRS Sir David Attenborough
4 October, 2023 RRS Sir David Attenborough
Traditionally when working in a remote environment, we fall back on wood and glue to repair and modify parts onboard the RRS Sir David Attenborough. Quite often, the plastic components that get damaged stay damaged until we can find the time to source, requisition and ship a replacement. This is something of a disadvantage! The shipping cost, time investment in locating and part cost for a small component can be unrealistic compared to the actual value of the part.
With 3D printing, parts can be custom made, replicated or invented to suit the requirements onboard at minimal cost. Where the product you need isn’t available, we can make to order in a variety of materials – for example fire axe blade covers in a flexible thermoplastic called TPU. We’ve even had some quite unique requirements, such as replacing metal-free brackets in clean laboratories.
We’ve traditionally relied upon carpenters and machinists to make the parts we need, but these are specialist trades and not always able to produce what we really require. 3D printing gives us more flexibility without requiring major investment in training.
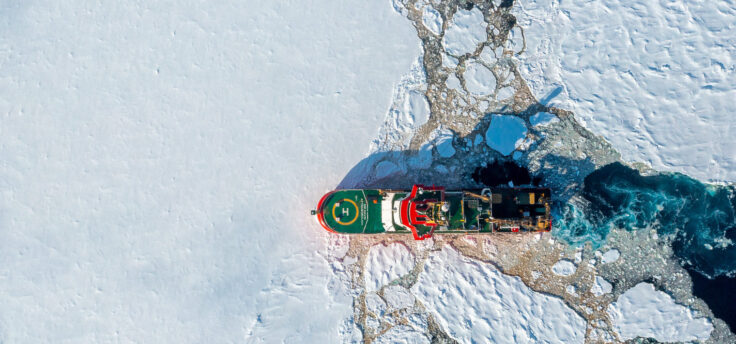
An added complication for developing the full potential of 3D printing on board a polar vessel such as the RRS Sir David Attenborough has been the limited band-width, which makes it very challenging to source templates for designs that aren’t already downloaded. Defend3D, as part of the Institute of Security, Science and Technology at Imperial College London, addresses this difficulty with their Virtual Inventory Communications Interface software.
Using a continuous, dynamic stream to a wide variety of manufacturing devices with bandwidths as low as 3kbps, enables a smooth printing process from a secure and centralised repository of engineer-grade parts across the BAS network. This allows the externalisation of IP protected parts to be printed in remote locations onboard the ship, even if bandwidth issues cause interruptions.
A recent example of using DEFEND3D’s software on the RRS Sir David Attenborough has been to print a bespoke part – a bracket to hold a peristaltic pump which originally was made in house to take controlled samples from salinometers. The software worked as expected without any challenges; it was an easy process to complete, and being able to 3D-print this part onboard meant it could be used straight away without any delays, and printed exactly to the bespoke design specifications.
It’s fair to say that you only really realise the full potential of this technology once you start using it and begin to understand that within the limits of the materials themselves, you can realise almost anything you can design on a computer.